Habitat for Humanity Kent County Chapter has been a leader and pioneer in the field when it comes to affordable and sustainable housing. In 2006, they built the nation’s first affordable LEED certified home under the LEED for Homes pilot project. Due the success of the first home, Habitat for Humanity Kent Co made an innovative commitment in 2007 – that future families would live in homes built to minimum LEED Silver Certification. Currently, they have surpassed the Silver level and have progressed to LEED Gold Certified Homes as their new standard house.
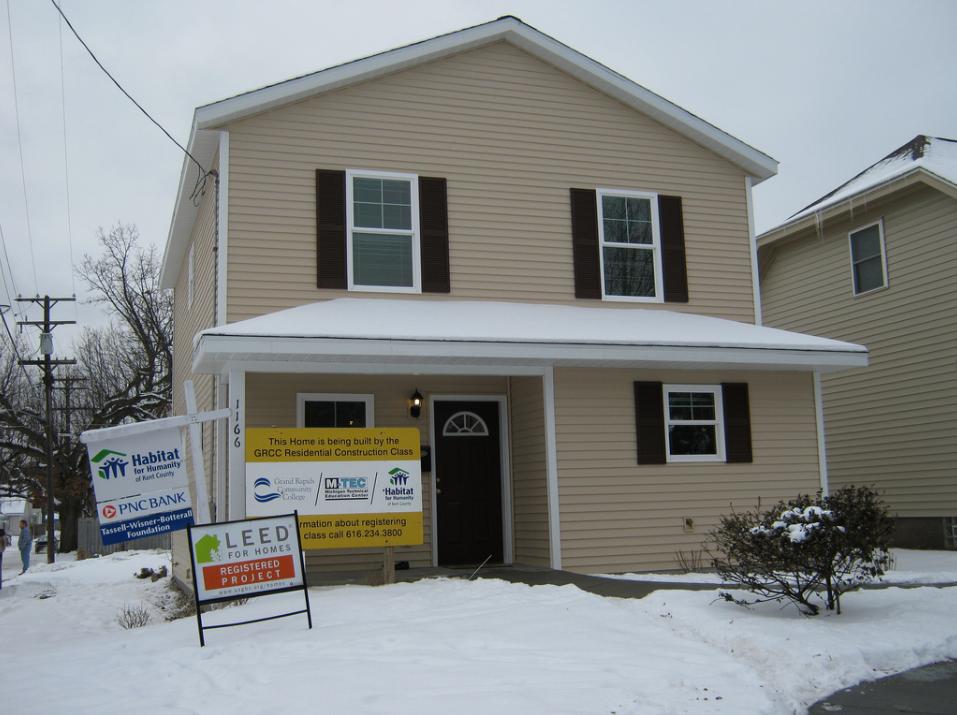
View/Download Complete project profile with LEED score and checklist here.
The Lee House was deconstructed and rebuilt after a fire had burned down the original home (see below). Habitat partnered with GRCC Tassell M-TEC students and instructor Duane McIntyre to build this 5-bedroom two story “Gervais” plan. It is “ZeroStep Certified” to be accessible, and also achieved LEED for Homes Gold Certification. Its 52 Home Energy Rating System score makes this one of Habitat Kent County’s most energy efficient home to date.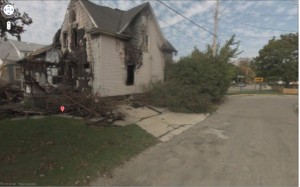
To date Habitat for Humanity Kent County has achieved great strides with LEED certification. They have built over 300 homes since they started in Kent County and certified 68 of those homes under the LEED rating system. They have registered 83 as of March 31st 2011 (with more to come!).
LEED Gut Rehabs of existing homes: 19
Average HERS score: 62.1
New Construction LEED Homes: 49
Average HERS score: 61.7
Average Square foot of Conditioned floor area: 1,750
This Habitat affiliate has built to the LEED standard in cities such as Sparta, Grand Rapids, Wyoming, Allendale, Cutlerville, Wayland all in Kent County, Michigan.
The latest home was a total gut-rehab project, made possible by the City of Grand Rapids and HUD via the Neighborhood Stabilization Project (NSP). It has achieved the coveted LEED for Homes Gold certification and will offer the hard-working Lee family a very energy efficient home.
A unique post and beam Generations timber frame porch made from reclaimed power poles will grace the front of this home– easily the most challenging rehab project HFHKC has undertaken.
View/Download Complete project profile with LEED score and checklist here.
Due to Habitat for Humanity of Kent Counties commitment to LEED certification, they have been able to attract many more sponsors, donors and volunteers. They have also been able to achieve some great accomplishments.
Deconstruction of homes literally saves tons of usable materials and items from heading to the landfill. These materials are re-sold at the Habitat ReStore for a profit to build other homes.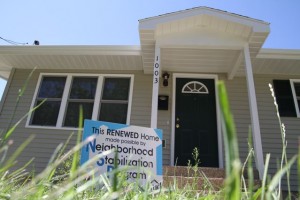
Thirty young construction students were educated in current green building practices and upon graduation, will bring those skills onto the local construction scene.
Habitat discovered that it costs approximately $8000 more to incorporate green building and zero-step entry into a Habitat home building per house, and that the long-term benefits to the family and the environment easily justify the expense.
It is estimated (based on their earliest LEED Homes) that annual savings costs for electric, water, and heating will be at least $1,000 per home per year. The extra money available every month eases the hard decision “food or heat?” for families who live close to the poverty line.
Over the life of each homebuyer’s 25 year mortgage, the savings equates to $25,000 at minimum – money a family is able to invest into strengthening their future.
The future looks bright for Habitat for Humanity and Green Building. They now have LEED Platinum and Zero Energy / Net Zero homes under-construction. They are partnering with over a dozen organizations to continue revitalization efforts in the Wealthy Heights Neighborhood of Grand Rapids. They may be looking towards LEED ND certification for their neighborhood redevelopment plans.